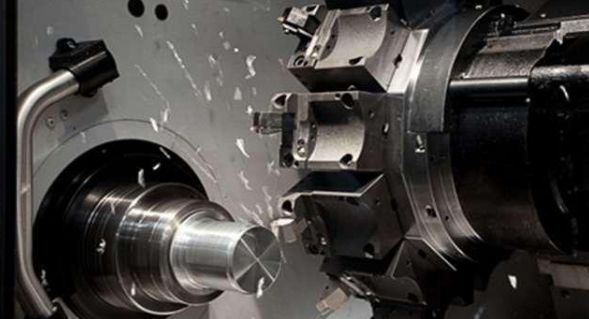
20世纪60年代为了适应核能、大规模集成电路、激光和航天等尖端技术的需要而发展起来的精度极高的一种加工技术。到80年代初,其最高加工尺寸精度已可达10纳米(1纳米=0.001微米)级,表面粗糙度达1纳米,加工的最小尺寸达 1微米,正在向纳米级加工尺寸精度的目标前进。纳米级的超精密加工也称为纳米工艺(nano-technology) 。超精密加工是处于发展中的跨学科综合技术。20 世纪 50 年代至 80 年代为技术开创期。20 世纪 50 年代末,出于航天、国防等尖端技术发展的需要,美国率先发展了超精密加工技术,开发了金刚石刀具超精密切削——单点金刚石切削(Single point diamond turning,SPDT)技术,又称为“微英寸技术”,用于加工激光核聚变反射镜、战术导弹及载人飞船用球面、非球面大型零件等。
南京NB88新博中心精密科技有限公司
如在加丁过程中对研抛工具形状、工件支撑状态以及加工参数等进行实时自适应控制,从而提高了加工精度和效率,发展成为“准确定性”超精密加工技术,这种方式是目前光学元件的主要加工方式,其中典型的准确定性超精密加工工艺包括小磨头抛光、磁流变抛光、气囊抛光、离子束抛光、应力盘抛光等,这些超精密加丁工艺可以通过控制驻留时间、压力、工件转速等参数确定去除函数,预知准确的材料去除量从而最终控制工件的面形(见图1-6(b))。
超精密加工
与非确定性超精密加工技术相比,准确定性超精密加T技术具有以下特点:
①对加工设备精度要求较高:由于加工过程中需要控制加工点和丁具的相对位置精度,所以要求加工设备具有较高的重复定位精度,一般要求在0.01mm左右即可满足使用要求;
②由于通过理论计算或试验可以得到加工过程的去除函数,所以较为准确地控制每次加工的去除量,通过对去除函数收敛性的分析仿真可以大大缩短加工周期,这样不仅提高了加丁精度,同时也缩短了加工效率、降低了生产成本;
③可以通过加工设备复杂的多轴运动控制工具的轨迹,进行包括非球面、自由曲面等复杂曲面超精密加工。
超精密切削加工
主要有超精密车削、镜面磨削和研磨等。在超精密车床上用经过精细研磨的单晶金刚石车刀进行微量车削,切削厚度仅1微米左右,常用于加工有色金属材料的球面、非球面和平面的反射镜等高精度、表面高度光洁的零件。例如加工核聚变装置用的直径为800毫米的非球面反射镜,最高精度可达0.1微米,表面粗糙度为Rz0.05微米。
超精密特种加工
加工精度以纳米,甚至最终以原子单位(原子晶格距离为0.1~0.2纳米)为目标时,切削加工方法已不能适应,需要借助特种加工的方法,即应用化学能、电化学能、热能或电能等,使这些能量超越原子间的结合能,从而去除工件表面的部分原子间的附着、结合或晶格变形,以达到超精密加工的目的。属于这类加工的有机械化学抛光、离子溅射和离子注入、电子束曝射、激光束加工、金属蒸镀和分子束外延等。这些方法的特点是对表面层物质去除或添加的量可以作极细微的控制。但是要获得超精密的加工精度,仍有赖于精密的加工设备和精确的控制系统,并采用超精密掩膜作中介物。例如超大规模集成电路的制版就是采用电子束对掩膜上的光致抗蚀剂(见光刻)进行曝射,使光致抗蚀剂的原子在电子撞击下直接聚合(或分解),再用显影剂把聚合过的或未聚合过的部分溶解掉,制成掩膜。电子束曝射制版需要采用工作台定位精度高达±0.01微米的超精密加工设备。